REVISTA ANUAL DEL GRUPO ATLAS COPCO
Sustainable technologies
Markets
Smart manufacturing
Our culture
Energy efficiency
result
Search
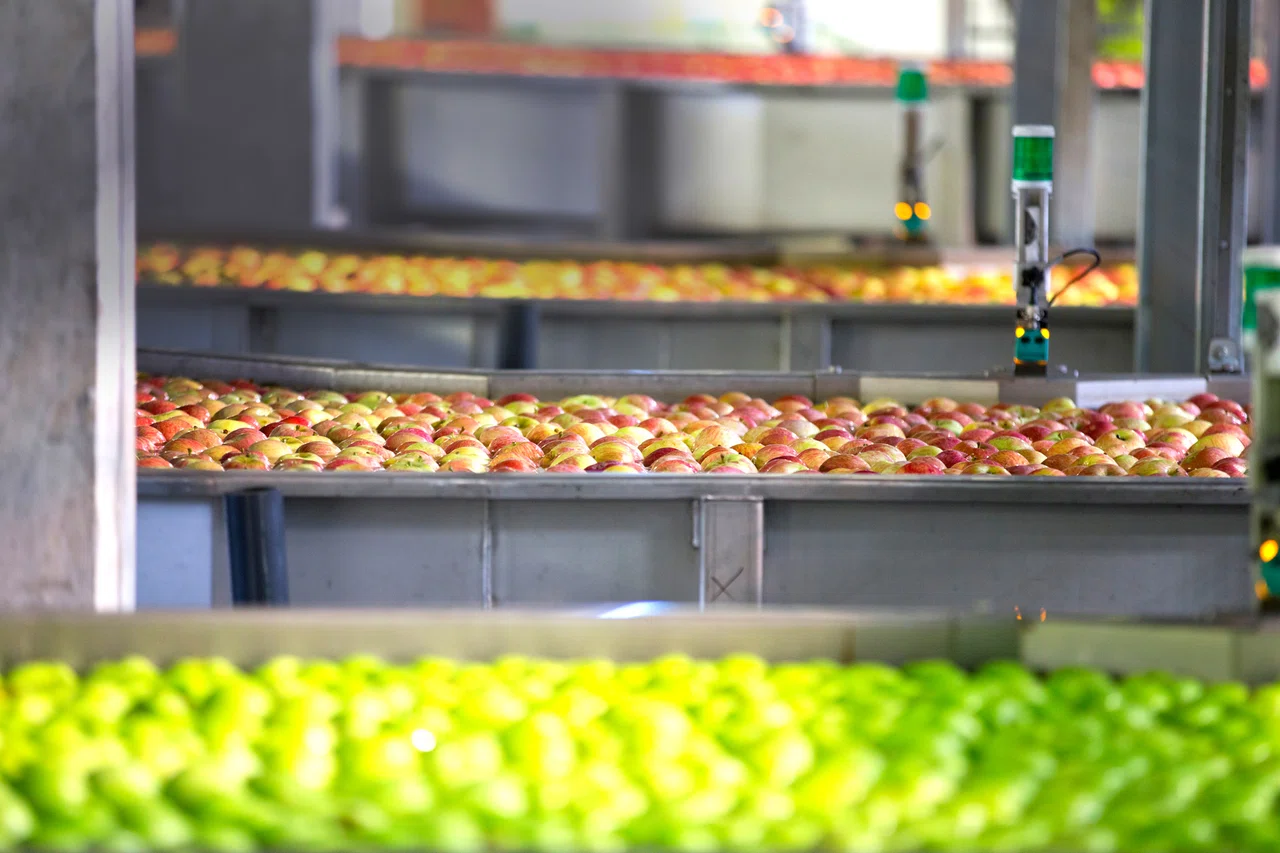
Convertir las manzanas en
puré de manzana
El aire comprimido es un requisito previo para la mayoría de los productos, servicios y herramientas que necesitamos a lo largo de la vida útil. Y todo comienza con pequeñas tarros de comida para bebé.
“Y no podemos costear el tiempo de inactividad. Con el sistema de conectividad proporcionado SMARTLINK, los expertos de mantenimiento de Atlas Copco y nosotros mismos monitoreamos los compresores de aire las 24 horas, los 7 días de la semana. Ahora puedo hablar con un empleado de servicio que se encuentra a 160 km de distancia y pedirle que mire los mismos datos de rendimiento que veo en las instalaciones”.
Geoff Martin
Equipo de mantenimiento de Néstle Gerber
La compañía de productos Gerber se fundó en 1927 como uno de los primeros productores de comida para bebé enlatada. Desde entonces, ha alimentado a generaciones de jóvenes estadounidenses. Hoy en día, la empresa es subsidiaria de Nestlé, pero Gerber sigue siendo una marca líder de alimento para bebés en el mercado estadounidense. Incluso tiene su “propio” bebé, incluido en todos los envases de los productos.
La planta de producción de Gerber en Fremont, Michigan, hace los purés de zanahorias, camotes, manzanas y otras frutas y verduras. Como los alimentos serán consumidos por bebés, la calidad y la seguridad son las prioridades principales. No debe haber ningún riesgo de que el producto tenga contacto incidental con el aceite, que suele estar presente en entornos industriales y, por lo tanto, los productores de alimentos deben buscar compresores de aire sin aceite. El proceso de producción de Gerber ya dependía de compresores sin aceite de Atlas Copco, por lo que cuando llegó el momento de subir un nivel del rendimiento energético, no tenían que mirar lejos para encontrar lo que necesitaban. Después de consultar al experto local en Atlas Copco, optaron por un compresor ZR 90-160 con VSD+, complementado con un secador MD.
“La razón por la que este compresor es tan atractivo para nosotros es que necesitamos un punto de condensación y un rendimiento de presión garantizados”, dice Geoff Martin, del equipo de mantenimiento de Gerber de Nestlé.
“Y no podemos costear el tiempo de inactividad. Con el sistema de conectividad proporcionado SMARTLINK, los expertos de mantenimiento de Atlas Copco y nosotros mismos monitoreamos los compresores de aire las 24 horas, los 7 días de la semana. Ahora puedo hablar con un empleado de servicio que se encuentra a 160 km de distancia y pedirle que mire los mismos datos de rendimiento que veo en las instalaciones”, Geoff continúa.
La fábrica solía tener cinco compresores de aire para toda la planta, pero al cambiar a un compresor mucho más eficiente, podían prescindir de tres de los compresores más antiguos y, en la actualidad, utilizar solo dos máquinas, el ZR 90 es uno de ellos. Ya que está equipado con la tecnología de variador de velocidad más sofisticada, ofrece importantes ahorros de energía, lo que se traduce en una reducción de los costos y un menor impacto ambiental.
“La ganancia en eficiencia energética que vemos es de aproximadamente 30 a 40 %, ya que nos permite apagar los secadores desecantes y otras máquinas que funcionarían durante horas sin cesar. Esta máquina hace todo lo que le pedimos y más”, concluye Geoff.
Artículos destacados
Síganos en:
Póngase en contacto con nosotros | Descargue el número de 2021/2022 | ©Atlas Copco AB