Síganos en:
Póngase en contacto con nosotros | Descargue el número de 2021/2022 | ©Atlas Copco AB
REVISTA ANUAL DEL GRUPO ATLAS COPCO
Sustainable technologies
Markets
Smart manufacturing
Our culture
Energy efficiency
result
Search
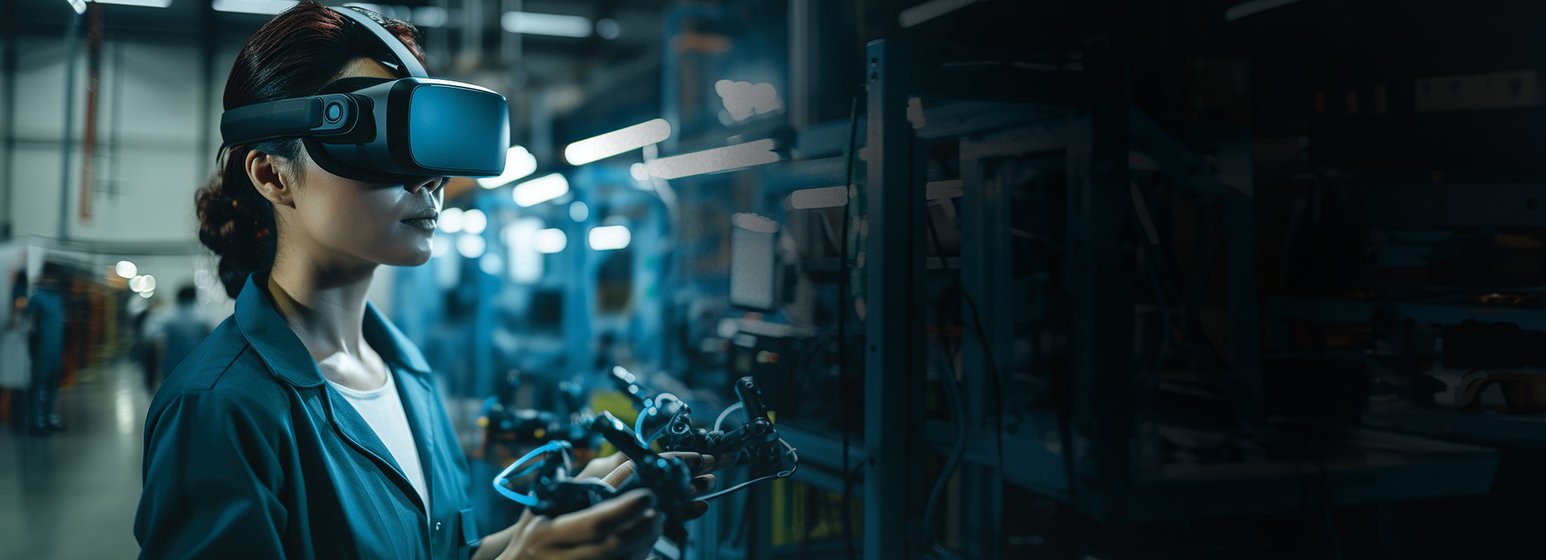
Una nueva y
fascinante realidad
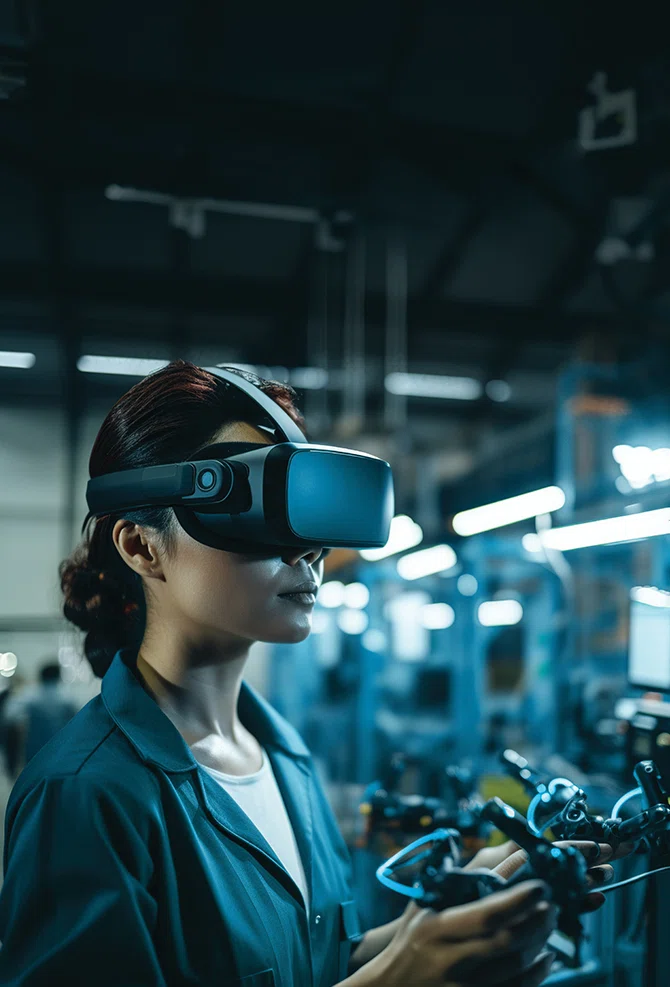
Las tecnologías de realidad extendida (XR, del inglés Extended Reality) son muy prometedoras para los productos y procesos del grupo Atlas Copco. El líder del grupo de XR, Wes Tomer, y algunos colegas pioneros explican cómo esto ayuda a los clientes y colegas.
Solían pertenecer al ámbito de los juegos de computadora y la ciencia ficción, pero las tecnologías de realidad extendida, como la realidad aumentada (RA) y la realidad virtual (RV), están transformando los procesos y productos industriales.
Atlas Copco ya está a bordo, con proyectos de XR en marcha en todas las áreas de nuestro negocio (consulte cuatro casos de estudio a continuación) y un grupo de XR que involucra a 150 personas en las cuatro áreas de negocio.
“La XR ofrece una forma potente y versátil de interactuar con modelos 3D de nuestros productos, explorarlos y permitir la colaboración entre expertos y aquellos que están aprendiendo”, explica Wes Tomer, gerente del programa de realidad extendida para las divisiones de Semiconductores en técnica de vacío. Wes educa a las personas sobre la tecnología y sobre cómo puede agregar valor comercial a Atlas Copco y a nuestros clientes.
La RA y la RV son adecuadas para nuestros lugares de trabajo digitalizados. La realidad aumentada superpone hologramas digitales 3D de los productos dentro del contexto real del usuario, mientras que la realidad virtual sumerge al usuario en el entorno 3D. Entre otras cosas, esto se traduce en una capacitación interactiva sobre herramientas y procesos complejos, y formas más rápidas y convenientes de conocer a las personas virtualmente y resolver los problemas de los usuarios de productos.
“Un técnico puede realizar un desmontaje completo de productos y procedimientos de servicio en RV sin muchos de los desafíos tradicionales. No es necesario viajar y no hay riesgo de dañar la máquina, perder piezas o afectar el proceso del cliente porque todo el procedimiento es virtual”, afirma Wes.
Si bien no pueden emular las ventajas únicas de la capacitación y el mantenimiento en persona, las tecnologías de XR son buenas para el negocio multinacional y la base de clientes de Atlas Copco. Wes Tomer está trabajando en varias iniciativas en torno a modelos de productos 3D dentro del área de negocios de técnicas de vacío, y planifica una prueba de concepto con software de RV con casos de uso de cada una de las cuatro áreas de negocios.
“La XR está haciendo avances significativos hacia una interacción más humana y natural con el mundo digital. Quiero ver a nuestros colegas y clientes acoger las posibilidades y los beneficios que esto trae”, comenta Wes.
Un técnico puede realizar un desmontaje completo de productos y procedimientos de servicio en RV sin muchos de los desafíos tradicionales. No es necesario viajar y no hay riesgo de dañar la máquina, perder piezas o afectar el proceso del cliente porque todo el procedimiento es virtual”,
Wes Tomer
Extended Reality Program Manager for Semiconductor divisions in Vacuum Technique
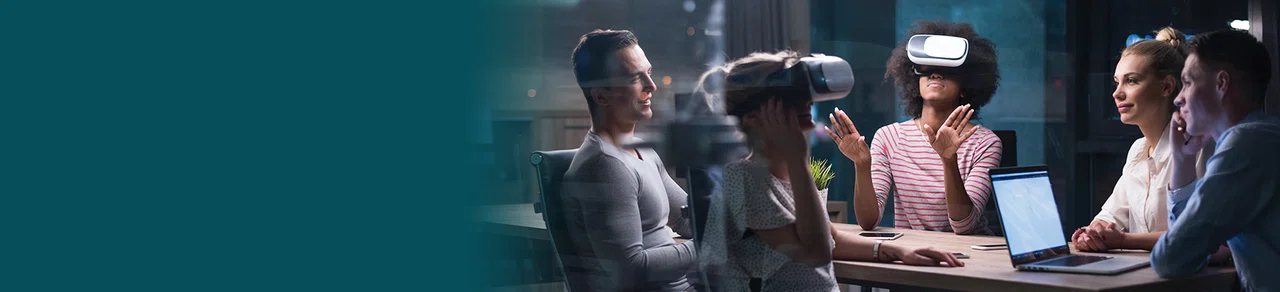
Cómo Atlas Copco está explorando la XR
Técnica de potencia: Parham Naderi
Durante los últimos dos años, el experto en procesos comerciales Parham Naderi ha liderado un proyecto que utiliza la RA y la RV para hacer que la revisión del diseño de productos sea más rápida y rentable.
Los revisores de diseño de Atlas Copco son responsables de mejorar la calidad, el rendimiento y la funcionalidad de un producto, y de reducir el riesgo de problemas durante el desarrollo del producto. Esto puede ser extenso y costoso, ya que los revisores de diseño pueden tener que viajar una larga distancia al sitio de Atlas Copco, donde se encuentra el producto, para realizar la evaluación.
Este proyecto está probando los “anteojos inteligentes” de la realidad aumentada Microsoft HoloLens. Cuando se combinan con un software personalizado, permiten realizar una “reunión de colaboración” en una sala virtual. Los revisores y los ingenieros de diseño pueden mirar la máquina juntos, de modo que los revisores pueden asesorar a los ingenieros de forma remota sobre lo que se debe realinear o cambiar.
“Solo usar HoloLens y mirar la máquina frente a nosotros reduce mucho el esfuerzo y los viajes al sitio”, dice Parham. “De esta manera, podríamos ahorrar dinero y reducir las emisiones de carbono”.
El proyecto aún se encuentra en etapa de validación del concepto con pruebas en Bélgica e India, pero Parham espera que su promesa inicial pase al siguiente paso a finales del 2023.
“Estoy entusiasmado con el potencial de esto”, comenta Parham.
Técnica de vacío: Richard Swayne
Las plantas de fabricación de semiconductores pueden ser lugares riesgosos para nuestros ingenieros de servicio en terreno porque trabajan en la fábrica de semiconductores, donde los subproductos químicos de la fabricación de obleas de silicio se aplacan y se hacen seguros.
Existe un régimen de seguridad estricto, pero la capacitación para ese entorno es difícil. Los módulos de PowerPoint tradicionales no proporcionan experiencia práctica, mientras que la creación de sistemas de gestión de escape integrados de réplica para el transporte en todo el mundo con fines de capacitación sería demasiado costosa y poco práctica.
Richard Swayne, jefe de Aprendizaje y Desarrollo para las divisiones de Semiconductores y Semiservicio, y su colega, Ondrej Hrudka, han desarrollado un software de capacitación piloto que crea una fábrica virtual de semiconductores. Los aprendices usan un casco de realidad virtual y navegan por un espacio virtual seguro para familiarizarse con los peligros y los controles de seguridad de una fábrica de semiconductores, lo que incluye duchas inmersivas, kits de primeros auxilios y teléfonos de emergencia.
“Es una forma de permitirles sentir que realmente están en una fábrica de semiconductores y experimentar las cosas que suceden alrededor de ellos sin el riesgo de hacerse daño físico”, explica Richard. “Navegan por el espacio y, luego, hay un módulo final en el que realizan una tarea típica de recolectar una bomba y moverla, con todos los peligros en juego.
“Es intenso, pero es un complemento importante y práctico para el rol de un instructor. Idealmente, no es recomendable que un aprendiz se capacite en un entorno en vivo y de alto riesgo, por lo que es mejor darle esa primera capacitación en el mundo virtual antes de llevarlo al mundo real”.
El concepto se está sometiendo a pruebas en Corea del Sur y en Estados Unidos, y Richard espera que los resultados positivos iniciales lleven a una adopción más amplia.
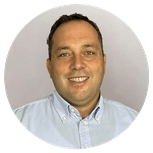
Técnica industrial: Nicolo’ Fioretti
Cualquier persona que tenga dificultades para construir muebles para el hogar podrá reconocer la frustración de seguir instrucciones.
Es aún más difícil para nuestros ingenieros de servicio en terreno, quienes consultan manuales para productos complejos y de alta calidad con tecnología avanzada mecánica, electrónica y de software. A veces, un técnico necesita ayuda de colegas especialistas, por lo que el cliente debe esperar días o semanas para obtener una solución.
Esto motivó a Nicolo' Fioretti, un gerente del equipo de Competencia con sede en Milán en el área de negocios de Técnica Industrial, a trabajar con PTC, socio de tecnología de diseño de Atlas Copco, para desarrollar una experiencia de realidad aumentada basada en dibujos de diseño asistido por computadora (CAD, del inglés Computer-Aided Design) de STBench.
“Nuestros ingenieros de servicio en terreno pueden acceder al CAD a través de una aplicación en sus teléfonos inteligentes. Ven nuestra representación 3D animada del producto frente a ellos, con instrucciones paso a paso sobre qué hacer. ¡Es como tener un instructor en su bolsillo!”
El equipo de Nicolo también ha utilizado la RA para mejorar la experiencia del usuario de los clientes. Creó un código QR para el folleto de STRwrench. Los clientes utilizan el código para descargar una aplicación con una vista previa en 3D de la funcionalidad del producto antes de comprarlo, o cuando tienen un producto y necesitan orientación.
“Al igual que con las animaciones 3D, usamos la RA para simplificar el proceso de aprendizaje, lo que ahorra tiempo a nuestros clientes. Puede dar un verdadero impulso de confianza a los ingenieros de servicio en terreno y a los clientes”.
El equipo de Nicolo ya está planificando más aplicaciones de RA y RV.
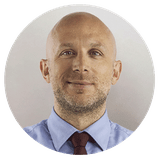
Técnica de compresores: Simone Rabadozza
En Montecchio Maggiore, Vicenza, Italia, Ceccato Aria Compressa, una empresa del grupo Atlas Copco, se asoció con investigadores de la Universidad de Padua para crear una simulación de un nuevo procedimiento de fabricación antes de trasladarse a una fábrica nueva y más grande.
Ceccato Aria Compressa se encarga del ensamblaje de compresores y la producción de secadores integrados, además de la fabricación de cartuchos de filtración para aire comprimido. Es uno de los sitios de producción de mayor volumen en todo el grupo y algunas de las unidades que se fabrican son ensambladas por algunas de nuestras otras empresas. El impacto de una parada de producción es inimaginable.
“Queríamos realizar muchos cambios en los flujos de producción de la nueva planta para obtener flexibilidad, capacidad y seguridad”, explica Simone Rabadozza, gerente de Fabricación con responsabilidad en el sitio y el hombre que lideró el proyecto.
“Estábamos buscando una manera de simular la nueva planta, los nuevos flujos y las nuevas operaciones, especialmente la logística, para ver los puntos en que se producirían los cuellos de botella y dónde estarían las limitaciones. También teníamos el objetivo de solucionar problemas potenciales antes de realmente construir de manera física la instalación y diseñar el flujo de trabajo.
“La universidad contaba con herramientas de RV que nos permitieron crear un gemelo digital completo de la fábrica basado en los datos reales: la producción, los flujos, las velocidades… todo. Una vez que determinamos el panorama marcador, pudimos posicionar todos los datos y ver dónde se presentaban los problemas: los puntos en que las líneas eran demasiado rápidas o demasiado lentas, si la recepción era buena o no, y así sucesivamente”.
Ceccato Aria Compressa se trasladó a la nueva fábrica en el 2022 y la simulación exitosa ayudó a garantizar una transición fluida a la producción continua de alta intensidad.
Artículos destacados