Folgen Sie uns auf:
Kontaktieren Sie uns | Ausgabe 2021/2022 herunterladen | ©Atlas Copco AB
DAS JÄHRLICHE MAGAZIN ATLAS COPCO GROUP
Sustainable technologies
Markets
Smart manufacturing
Our culture
Service and Consulting
Energy efficiency
result
Search
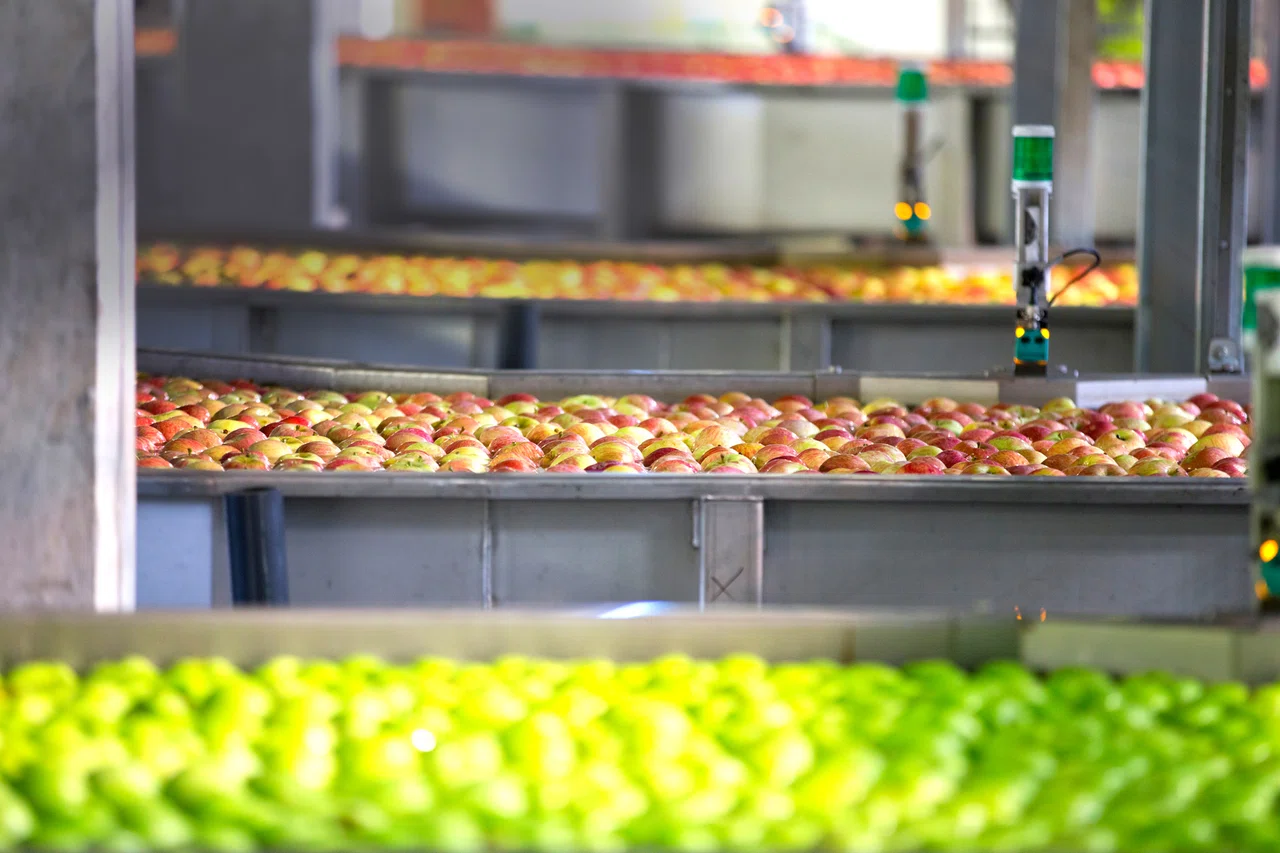
Äpfel in
Apfelmus verwandeln
Druckluft ist eine Voraussetzung für die meisten Produkte, Dienstleistungen und Werkzeuge, die wir im Leben benötigen. Alles beginnt mit kleinen Gläsern mit Babynahrung.
We cannot afford to have downtime. With the provided SMARTLINK connectivity system our air compressors are monitored 24/7 by Atlas Copco’s maintenance experts as well as ourselves. I can now talk to a service guy sitting 100 miles away and ask him to look at the same performance data I see on-site”
Geoff Martin
Néstle Gerber Maintenance team
Die Gerber Products Company wurde 1927 als einer der ersten Hersteller von Babynahrung aus der Dose gegründet. Seitdem hat es Generationen von jungen Amerikanern ernährt. Das Unternehmen ist heute eine Tochtergesellschaft von Nestlé und nach wie vor eine führende Marke für Babynahrung auf dem US-Markt. Es hat sogar sein „eigenes“ Baby, das auf allen Produktverpackungen zu finden ist.
In der Produktionsanlage von Gerber in Fremont, Michigan, werden Pürees aus Karotten, Süßkartoffeln, Äpfeln und anderen Früchten und Gemüsen hergestellt. Da diese Nahrung Kleinkindern serviert wird, stehen Qualität und Sicherheit an erster Stelle. Es muss ausgeschlossen werden, dass das Produkt unbeabsichtigt mit Öl aus industriellen Umgebungen in Kontakt kommt, und die Lebensmittelhersteller entscheiden sich daher zumeist für ölfreie Kompressoren. Der Produktionsprozess von Gerber basierte bereits auf ölfreien Kompressoren von Atlas Copco. Als es an der Zeit war, die Energieleistung zu verbessern, musste man nicht lange suchen, um das zu finden, was man brauchte. Nach Rücksprache mit dem Atlas Copco-Experten vor Ort fiel die Wahl auf einen ZR 90-160 VSD+-Kompressor, ergänzt durch einen MD-Trockner.
„Der Grund, warum dieser Kompressor für uns so attraktiv ist, ist, dass wir einen garantierten Taupunkt und eine garantierte Druckleistung benötigen“, sagt Geoff Martin vom Néstle Gerber-Wartungsteam.
„Und wir können uns keine Ausfallzeiten leisten. Mit dem zur Verfügung gestellten SMARTLINK-Verbindungssystem werden unsere Druckluftkompressoren rund um die Uhr von den Wartungsexperten von Atlas Copco sowie von uns selbst überwacht. Ich kann jetzt mit einem Servicetechniker sprechen, der über 100 Kilometer entfernt ist, und ihn bitten, sich die gleichen Leistungsdaten anzusehen, die ich vor Ort sehe“, fährt Geoff fort.
Früher hatte das Werk fünf Druckluftkompressoren, die die gesamte Anlage versorgten. Durch die Umstellung auf ein wesentlich effizienteres Kompressormodell konnten drei der älteren Kompressoren ausgemustert werden, sodass jetzt nur noch zwei Maschinen im Einsatz sind. Eine davon ist die ZR 90. Da diese mit der modernsten drehzahlvariablen Antriebstechnologie ausgestattet ist, sorgt sie für erhebliche Energieeinsparungen, was zu geringeren Kosten und weniger Umweltbelastungen führt.
„Die Energieeffizienzsteigerung liegt bei etwa 30 bis 40 %, da wir die Adsorptionstrockner und andere Maschinen, die stundenlang in Betrieb wären, jetzt abschalten können. Diese Maschine kann alles, was wir von ihr verlangen, und noch viel mehr“, schließt Geoff.