Folgen Sie uns auf:
Kontaktieren Sie uns | Ausgabe 2021/2022 herunterladen | ©Atlas Copco AB
DAS JÄHRLICHE MAGAZIN ATLAS COPCO GROUP
Sustainable technologies
Markets
Smart manufacturing
Our culture
Service and Consulting
Energy efficiency
result
Search
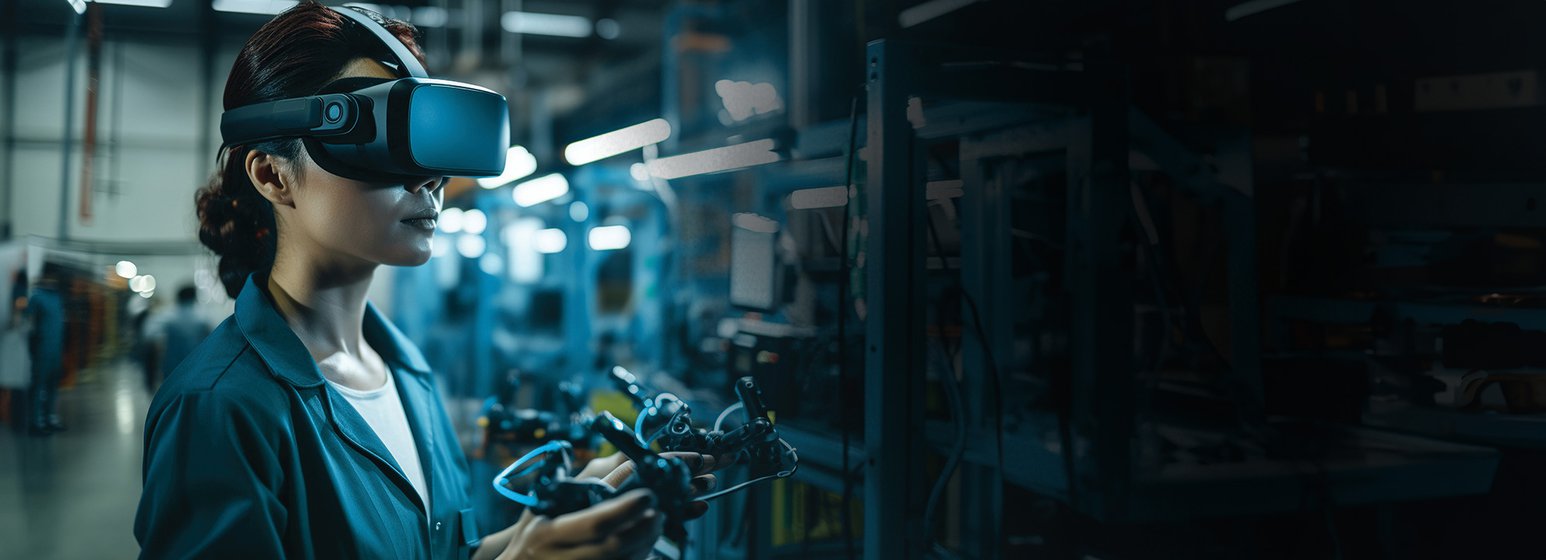
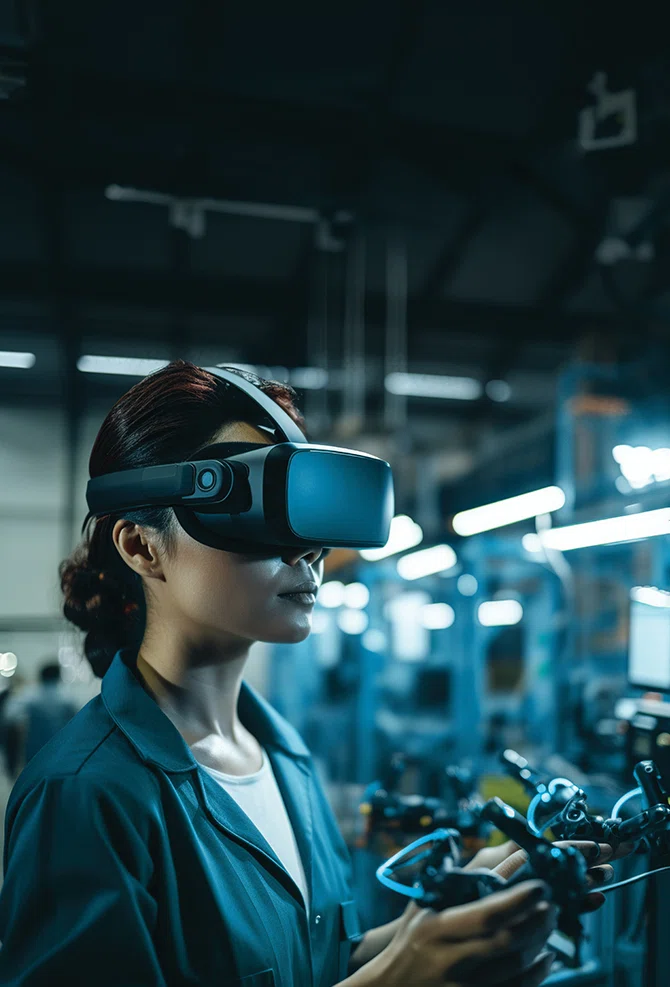
Eine spannende
neue Realität
Extended Reality-Technologien (XR) bieten großes Potential für die Produkte und Prozesse der Atlas Copco Group. Wes Tomer, Leiter der XR Group, und einige Kollegen, die in diesem Bereich Pionierarbeit leisten, erläutern, welchen Nutzen diese Technologien für Kunden und Kollegen haben können.
Einst ausschließlich in Computerspielen und Science-Fiction anzutreffen, verändern Extended Reality-Technologien wie Augmented Reality (AR) und Virtual Reality (VR) heute auch industrielle Prozesse und Produkte.
Atlas Copco macht sich das mit XR-Projekten in unseren verschiedenen Geschäftstätigkeiten (siehe vier Fallstudien unten) und einer XR Group mit 150 Mitarbeitern aus allen vier Geschäftsbereichen bereits zunutze.
„XR bietet eine leistungsstarke und vielseitige Möglichkeit, mithilfe von 3D-Modellen unsere Produkte kennenzulernen und die Zusammenarbeit zwischen Experten und Auszubildenden zu ermöglichen“, erklärt Wes Tomer, Extended Reality Program Manager für die Semiconductor Division im Geschäftsbereich Vacuum Technique. Tomer bringt seinen Mitarbeitern die Technologie näher und zeigt ihnen den geschäftlichen Mehrwert für Atlas Copco und unsere Kunden auf.
AR und VR eignen sich hervorragend für unsere digitalisierten Arbeitsplätze. Augmented Reality überlagert digitale 3D-Hologramme von Produkten im realen Kontext des Benutzers, während Virtual Reality den Benutzer in die 3D-Umgebung eintauchen lässt. Dies ermöglicht unter anderem interaktive Schulungen zu komplexen Werkzeugen und Prozessen sowie schnellere und bequemere Möglichkeiten, sich virtuell zu treffen und Benutzerprobleme zu lösen.
„Ein Techniker kann Demontage- und Wartungsarbeiten vollständig in VR durchlaufen, ohne die vielen altbekannten Herausforderungen bewältigen zu müssen. Reisen sind nicht erforderlich, und es besteht keine Gefahr, dass die Maschine beschädigt wird, Teile verloren gehen oder der Prozess des Kunden beeinträchtigt wird, da das gesamte Verfahren virtuell abläuft“, so Tomer.
Auch wenn sie die besonderen Vorteile von Präsenzschulungen und Serviceleistungen nicht bieten können, eignen sich XR-Technologien hervorragend für die multinationalen Geschäftstätigkeiten und Kunden von Atlas Copco. Wes Tomer arbeitet an mehreren Initiativen zu 3D-Produktmodellen im Geschäftsbereich Vacuum Technique und plant die Durchführung eines Machbarkeitsnachweises mit VR-Software und Anwendungsfällen aus allen vier Geschäftsbereichen.
„XR macht bemerkenswerte Fortschritte in Richtung einer menschlicheren und natürlicheren Interaktion mit der digitalen Welt. Ich möchte, dass unsere Kollegen und Kunden von den Möglichkeiten und Vorteilen profitieren können, die dies mit sich bringt“, erklärt er.
Ein Techniker kann Demontage- und Wartungsarbeiten vollständig in VR durchlaufen, ohne die vielen altbekannten Herausforderungen bewältigen zu müssen. Reisen sind nicht erforderlich, und es besteht keine Gefahr, dass die Maschine beschädigt wird, Teile verloren gehen oder der Prozess des Kunden beeinträchtigt wird, da das gesamte Verfahren virtuell abläuft“,
Wes Tomer
Extended Reality Program Manager for Semiconductor divisions in Vacuum Technique
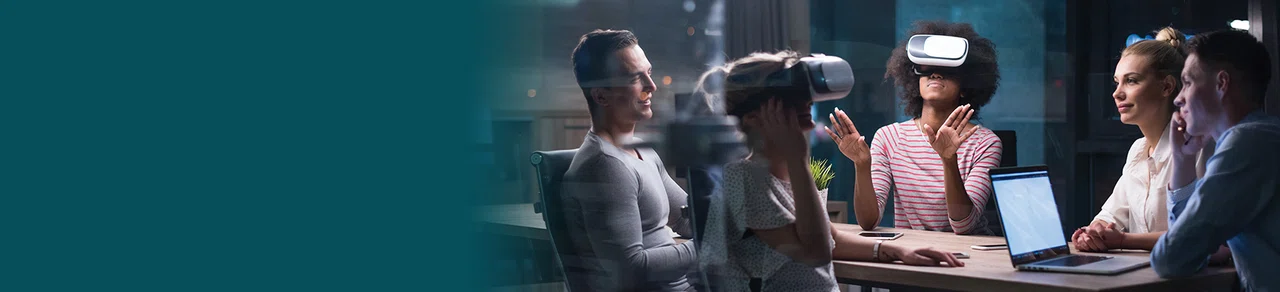
Atlas Copco und die XR-Technologie
Power Technique: Parham Naderi
In den letzten zwei Jahren leitete Business Process Expert Parham Naderi ein Projekt, das AR und VR nutzt, um die Überprüfung von Produktdesigns schneller und kostengünstiger zu gestalten.
Die Designprüfer von Atlas Copco sind dafür verantwortlich, die Qualität, Leistung und Funktionalität eines Produkts zu verbessern und das Risiko von Problemen während der Produktentwicklung zu verringern. Dies kann langwierig und kostspielig sein, da sie möglicherweise lange Wege zum Atlas Copco-Standort, an dem sich das Produkt befindet, zurücklegen müssen, um die Einschätzung vorzunehmen.
In diesem Projekt wird die HoloLens, die Augmented Reality-Brille von Microsoft, auf den Prüfstand gestellt. In Kombination mit einer speziellen Software ermöglicht sie die Zusammenarbeit in einem virtuellen Meetingraum. Designprüfer und Ingenieure können die Maschine zusammen begutachten, sodass die Designprüfer die Ingenieure aus der Ferne darüber informieren können, wenn etwas neu ausgerichtet oder geändert werden muss.
„Durch die Verwendung der HoloLens sehen wir die Maschine mit unseren eigenen Augen ohne größeren Aufwand, insbesondere für die Anreise“, so Naderi. „Auf diese Weise könnten wir Geld sparen und die CO₂-Emissionen reduzieren.“
Das Projekt wird noch mit Tests in Belgien und Indien auf seine Machbarkeit geprüft, doch Naderi ist positiv gestimmt, dass sich aus dem vielversprechenden ersten Eindruck bis Ende 2023 weitere Schritte ergeben werden.
„Das Potential ist enorm“, sagt er.
Vacuum Technique: Richard Swayne
Anlagen für die Halbleiterfertigung können für unsere Außendiensttechniker Risiken darstellen, da sie in den Sub-Fab-Bereichen arbeiten, in denen chemische Nebenprodukte der Siliziumwafer-Herstellung abgebaut und sicher gemacht werden.
Es muss ein strenges Sicherheitsprotokoll befolgt werden, doch Schulungen für diese Bereiche sind schwierig umzusetzen. Mit herkömmlichen PowerPoint-Schulungen lassen sich keine praktischen Erfahrungen sammeln, und die Errichtung von nachgebildeten integrierten Abgasmanagementsystemen für den weltweiten Transport zu Schulungszwecken ist zu teuer und aufwendig.
Richard Swayne, Head of Learning and Development für die Semiconductor Division und die Semi-Service Division, und sein Kollege Ondrej Hrudka haben eine Pilot-Schulungssoftware entwickelt, die eine virtuelle Sub-Fab erzeugt. Die Lernenden tragen ein Virtual Reality-Headset, navigieren durch einen sicheren, virtuellen Raum und machen sich mit den Gefahren und Sicherheitskontrollen vertraut, einschließlich immersiver Dusche, Erste-Hilfe-Kasten und Notruftelefon.
„Wir können ihnen so das Gefühl vermitteln, dass sie sich tatsächlich in einem Sub-Fab befinden, und dass Dinge um sie herum passieren, ohne dass sie körperlich Schaden nehmen können“, erklärt Swayne. „Sie bewegen sich durch den Raum und im Abschlussmodul müssen sie eine typische Arbeit wie das Entleeren und Bewegen einer Pumpe ausführen, einschließlich aller möglichen Gefahren, die damit verbunden sind.“
„Es ist eine intensive Erfahrung, aber es ist eine wichtige und praktische Ergänzung der Ausbildung. Idealerweise sollten keine Lernenden in einer realen, risikoreichen Umgebung lernen müssen. Lassen wir sie also das erste Training in der virtuellen Welt absolvieren, bevor wir sie in die reale Welt entlassen.“
Das Konzept wird derzeit in Südkorea und den USA erprobt, und Swayne hofft, dass erste positive Ergebnisse zu einer breiteren Akzeptanz führen werden.
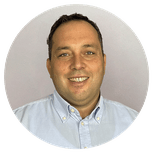
Industrial Technique: Nicolo’ Fioretti
Jeder, der schon einmal Möbel selbst aufgebaut hat, weiß, wie schwierig Anleitungen zu lesen sein können.
Für unsere Außendiensttechniker, die Handbücher für komplexe, hochwertige Produkte mit fortschrittlicher Mechanik, Elektronik und Software lesen müssen, ist dies noch schwieriger. Manchmal benötigt ein Techniker Hilfe von sachkundigen Kollegen, sodass der Kunde tage- oder wochenlang auf eine Lösung warten muss.
Dies motivierte Nicolo’ Fioretti, Competence Team Manager im Geschäftsbereich Industrial Technique aus Mailand, mit dem Konstruktionstechnologiepartner PTC von Atlas Copco zusammenzuarbeiten, um eine Augmented Reality-Erfahrung basierend auf den CAD-Zeichnungen der STBench zu entwickeln.
„Unsere Außendiensttechniker können über eine App auf ihrem Smartphone auf das CAD zugreifen. Vor sich sehen sie unsere animierte 3D-Darstellung des Produkts mit Schritt-für-Schritt-Anweisungen. Es ist, als hätte man immer einen Trainer dabei!“
Das Team um Fioretti hat AR auch eingesetzt, um die Benutzererfahrung für Kunden zu verbessern. Mit einem QR-Code auf der Broschüre des STRwrench können Kunden eine App mit einer 3D-Vorschau der Produktfunktionen herunterladen, bevor sie das Produkt kaufen oder wenn sie das Produkt bereits erworben haben und Hilfe benötigen.
„Wie bei den 3D-Animationen verwenden wir AR, um den Lernprozess zu vereinfachen und unseren Kunden Zeit zu sparen. Dies kann sowohl den Außendiensttechnikern als auch den Kunden einen echten Vertrauensschub geben.“
Das Team um Fioretti plant bereits weitere AR- und VR-Anwendungen.
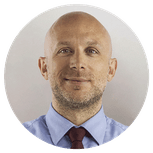
Compressor Technique: Simone Rabadozza
In Montecchio Maggiore, Vicenza, Italien, arbeitete das Unternehmen Ceccato Aria Compressa der Atlas Copco Group mit Forschern der Universität Padua zusammen an der Simulation eines neuen Herstellungsverfahrens für eine neue, größere Anlage.
Ceccato Aria Compressa baut Kompressoren und produziert integrierte Trockner sowie Filterpatronen für Druckluft. Es ist einer der Produktionsstandorte mit dem größten Produktionsvolumen in der gesamten Gruppe, und einige der hergestellten Einheiten werden später von unseren anderen Unternehmen genutzt. Die Folgen eines Produktionsstopps würden große Ausmaße annehmen!
„Wir wollten viele Änderungen an den Produktionsabläufen für die neue Anlage vornehmen, um so an Flexibilität, Kapazität und Sicherheit zu gewinnen“, erklärt Simone Rabadozza, Manufacturing Manager mit Verantwortung für den Standort und Projektleiter.
„Wir suchten nach einer Möglichkeit, die neue Anlage, die neuen Strukturen und die neuen Betriebsabläufe – insbesondere die Logistik – zu simulieren, um zu sehen, wo Engpässe und Einschränkungen bestehen könnten, und um potenzielle Probleme zu beheben, bevor die Anlage tatsächlich gebaut und der Betriebsablauf entworfen wird.
„Die Universität verfügte über VR-Tools, die es uns ermöglichten, auf der Grundlage von realen Daten – Leistungsabgabe, Strukturen, Geschwindigkeiten – einen vollständigen digitalen Klon der Anlage zu erstellen. Nachdem wir uns für das Musterszenario entschieden hatten, konnten wir alle Daten einspeisen und sehen, wo Probleme auftraten, d. h. wo die Linien zu schnell oder zu langsam arbeiteten, ob die Aufnahme gut funktionierte usw.“
Ceccato Aria Compressa zog 2022 in die neue Anlage um und durch die erfolgreiche Simulation lief der Übergang bei kontinuierlicher Produktion mit hohem Volumen reibungslos ab.
Vorgeschlagene Artikel