Follow us on:
CONTACT US | Download the 2021/2022 issue | ©Atlas Copco AB
result
Search
A MAGAZINE FROM ATLAS COPCO GROUP
Sustainable technologies
Markets
Smart manufacturing
Our culture
Service and Consulting
Energy efficiency
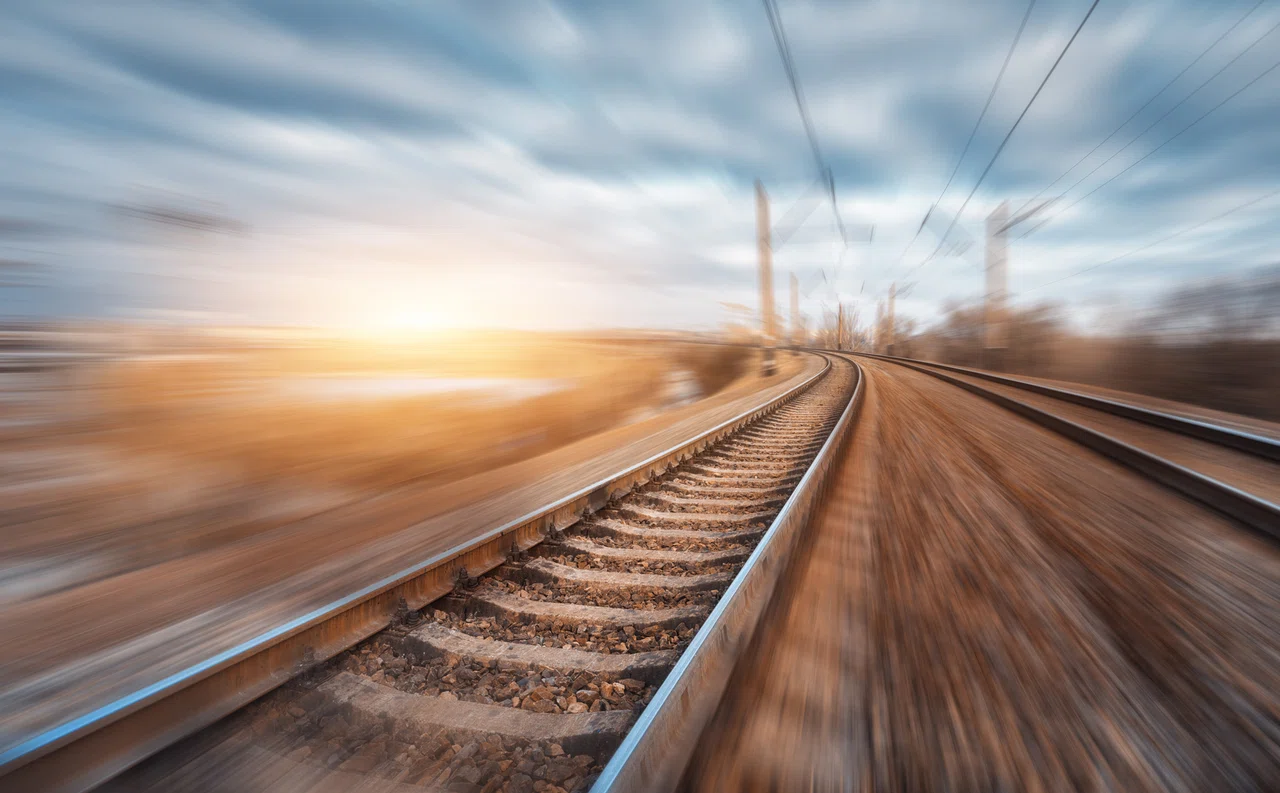
WHEN
TRAIN BEATS
THE PLANE
A pilot project for rail freight between Atlas Copco’s industrial vacuum production facility in Germany and its counterpart in China shows that rail transport can balance costs, speed and sustainability better than air and ocean freight.
Our strategy to switch to rail is driven by environmental and cost optimization needs, but it is also based on customer requirements.”
Alexander Irchin
Logistics Manager,
Atlas Copco Vacuum Technique
Atlas Copco’s commitment to growing in the right way underpins the green logistics strategy of the Group’s Industrial Vacuum division. But there’s always a challenge to balance fast deliveries, transportation costs and minimal environmental impact.
Leybold, a leading vacuum producer based in Cologne, Germany, sends heavy pumps weighing more than 150 kilograms, plus semi-finished parts such as components and rotors, to Tianjin, China, for local production and distribution. Although air cargo transports are quickest, at 10 days or less, the growing volumes to the Far East meant planes had become unsustainable, as Alexander Irchin, Logistics Manager, Atlas Copco Vacuum Technique, explains.
“We wanted to move away from using air freight as rail transportation is more economical. We were also concerned about the high levels of CO2 emissions produced through air transportation.”
Finding a new way
China’s heavy investment in the Belt and Road infrastructure project across Asia, and in the German port of Duisburg, has been a game changer for rail travel between China and Europe. Leybold therefore decided to make a rail freight pilot.
The "Lighthouse project" began in mid-2019, when 20 full container loads were sent by rail nearly 8 000 kilometers from Germany to China. In 2020, Leybold sent 74 containers of Rail cargo to Shanghai and Tianjin. The flow is arranged so that the full container load first goes to the production facility, where the team unloads the relevant goods before dispatching a truck onward to the customer center.
The benefits of train transports are clear. On this particular route, rail freight is 75% less costly than air freight, while the train's carbon emissions are 90% lower. Compared to ocean freight, the train is 50% quicker as the distance by rail is 8 000 kilometers compared to more than 23 000 kilometers by ocean.
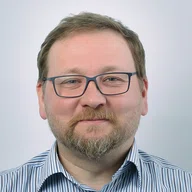
Jiri Polasek
European Distribution
Center Manager,
Edwards Czech Republic
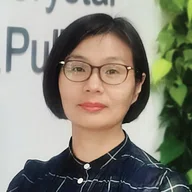
Rena An
Order Management
and Planning Manager,
Leybold China
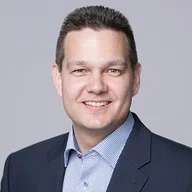
Alexander Irchin
Logistics Manager,
Atlas Copco Vacuum Technique
Securing the load
During the pilot, all Leybold’s transports were put in ocean freight packaging to avoid corrosion, while reducing the amount of plywood and completely eliminating the need for polyurethane foam. The transports were monitored via GPS tracker and the cargo’s temperature, humidity and load shocks were measured.
There can be significant temperature and humidity fluctuations, and load vibrations, but no significant damage was reported. This data prompted a decision to switch to rail for all but the heaviest of cargoes, which still go by container ship.
When distances are long, the planning time is important to ensure local market expectations can be met. Supply chain strategies focusing on planning delivery times, covering manufacturing and transport, are key to managing the right level of inventory for local markets and "just in time" refilling.
Another Europe-to-China rail route is now running in Edwards, also part of the Atlas Copco Group. Its distribution center in Czech Slavonin has started to ship products to destinations in Shanghai and Qingdao, via Poland. "We have also establishes rail shipments from China to European customers from our manufacturing center in Qingdao," Alexander says. "In addition to saving time and money, this also brings a reduction in CO2 emissions and on top of that improves customer satisfaction."
“Our strategy to switch to rail is driven by environmental and cost optimization needs, but it is also based on a strong focus on customer requirements. We wanted to establish a method that would get products to them without undue delay. It also proved to be a wise choice from a flexibility point of view. When we initiated this project we had no idea a global pandemic would hit, with logistics constraints and restrictions to follow. By using alternative and reliable transport modes like rail we were able to maintain supply and customer support in a very challenging time,” Alexander Irchin concludes.