Follow us on:
CONTACT US | Download the 2021/2022 issue | ©Atlas Copco AB
result
Search
A MAGAZINE FROM ATLAS COPCO GROUP
Sustainable technologies
Markets
Smart manufacturing
Our culture
Service and Consulting
Energy efficiency
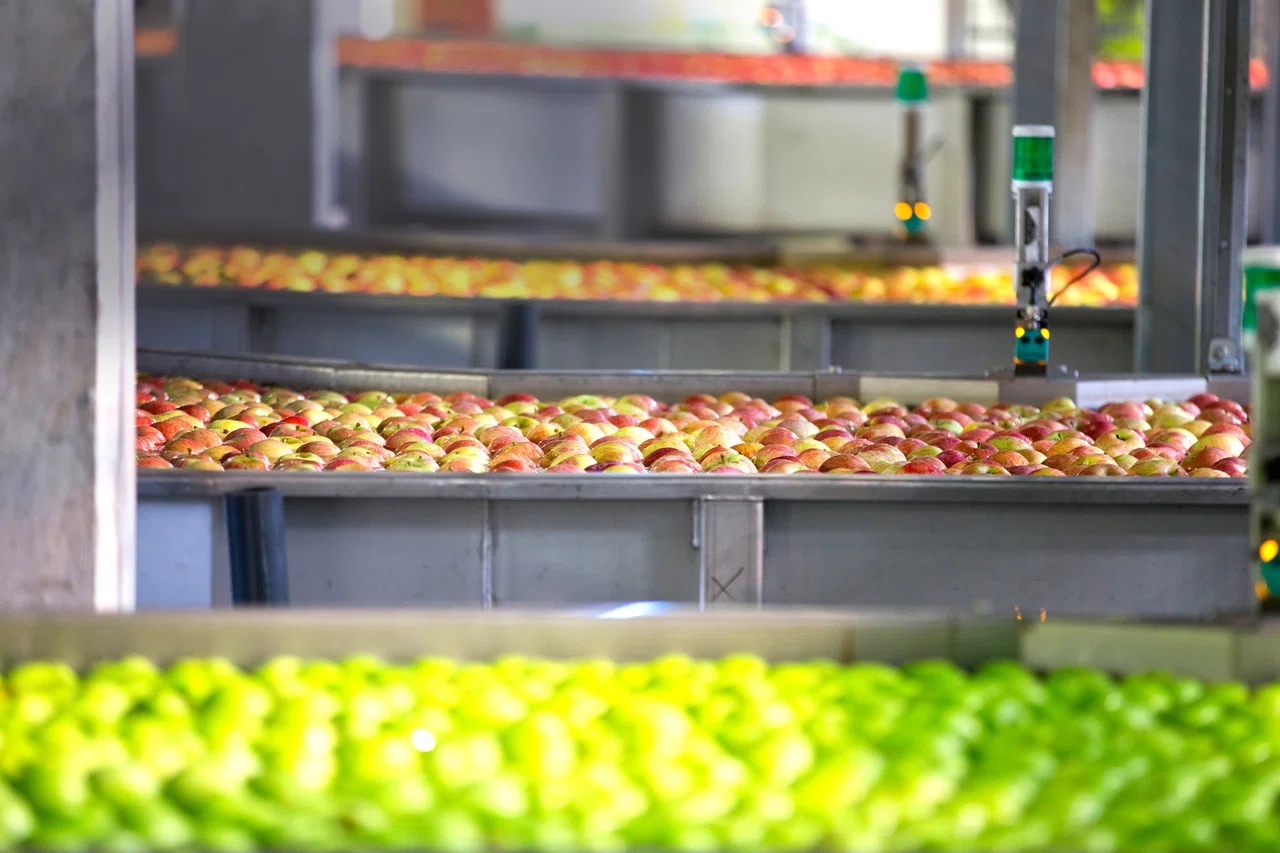
Turning apples into
APPLESAUCE
Compressed air is a prerequisite for most of the products, services and tools we need throughout life. And it all starts with small jars of baby food.
We cannot afford to have downtime. With the provided SMARTLINK connectivity system our air compressors are monitored 24/7 by Atlas Copco’s maintenance experts as well as ourselves. I can now talk to a service guy sitting 100 miles away and ask him to look at the same performance data I see on-site”
Geoff Martin
Néstle Gerber Maintenance team
The Gerber Products Company was founded in 1927 as one of the first producers of canned baby food. Since then, it has fed generations of young Americans. The company is nowadays a subsidiary of Nestlé, but Gerber remains a leading baby food brand on the U.S. market. It even has its “own” baby, featured on all product packaging.
Gerber’s production plant in Fremont, Michigan, makes purees of carrots, sweet potatoes, apples and other fruits and vegetables. As the food is served to infants, quality and safety are top priorities. There must not be any risk of the product having incidental contact with oil, which is frequently present in industrial settings, and food producers therefore go for oil-free air compressors. Gerber’s production process already relied on oil-free compressors from Atlas Copco, so when the time came to take energy-performance up a notch, they didn’t have to look far to find what they needed. After consulting their local Atlas Copco expert, their choice fell on a ZR 90-160 VSD+ compressor, complemented by an MD dryer.
“The reason this compressor is so appealing to us is that we need a guaranteed dew point and guaranteed pressure performance,” says Geoff Martin from the Néstle Gerber Maintenance team.
“And we cannot afford to have downtime. With the provided SMARTLINK connectivity system our air compressors are monitored 24/7 by Atlas Copco’s maintenance experts as well as ourselves. I can now talk to a service guy sitting 100 miles away and ask him to look at the same performance data I see on-site,” Geoff continues.
The factory used to have five air compressors serving the entire plant, but by switching to a much more efficient compressor, they were able to trim out three of the older compressors and now only use two machines, the ZR 90 being one of them. Since it’s equipped with the most sophisticated variable speed drive technology, it brings substantial energy savings, which means reduced costs and less environmental impact.
“The energy efficiency gain we see is around 30-40%, as we were able to shut down desiccant dryers and other machines that would be running for hours on end. This machine does everything we ask it to do, and more," Geoff concludes.