Follow us on:
CONTACT US | Download the 2021/2022 issue | ©Atlas Copco AB
result
Search
A MAGAZINE FROM ATLAS COPCO GROUP
Sustainable technologies
Markets
Smart manufacturing
Our culture
Service and Consulting
Energy efficiency
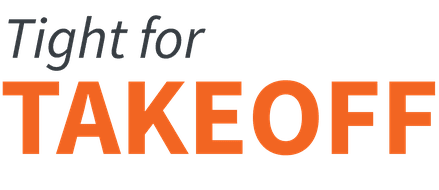
In a smart assembly environment, you need smart tools. With an integrated controller, advanced ergonomics and sustainable battery power, the Tensor IxB tightening tools are all that and more.
Connectivity is making the world of manufacturing digital, flexible and more sustainable, but for automotive or aerospace assembly plants, it’s a double-edged sword. Increasing consumer demands, tougher sustainability regulations and constant technical updates mean car manufacturers must regularly reconfigure or "rebalance" parts of their assembly lines. A single assembly station can easily take nine hours to rebalance. When you consider that manufacturers can have hundreds of stations, that’s a lot of time and money.
The aerospace industry must respond to its own technical, consumer and regulatory demands. Tightening deviations, often stemming from the tendency to use cheaper air or battery-powered basic clutch tools, can have implications on both safety and cost control. If tightening errors are missed, the cost of reworking can be tens of thousands of euros. And the use of more advanced tools can be hindered by their lack of ergonomics and stable wire connection in cramped, hard-to-reach parts of the aircraft.
But Atlas Copco’s Tensor IxB cordless tools are about to turn the tightening tool market upside down. “We saw several years ago that there was a need for increased flexibility” says Jonas Mann, Vice President R&D for tools and assembly systems. “It is labor-intensive to rebalance a line and move a controller box from one station to another. You must unscrew it from a rack, move it physically and draw new cables to make network drops and connect it to the system. You basically have to stop the line or incur the expense of doing it over a weekend. But with a Tensor IxB tool you can do it almost ‘on the fly.’”
“Tensor IxB is a range of tightening tools that fits really well with the smart factory concept,” says Tim Mann, Global Product Manager for the Tensor IxB Family (who is not related to Jonas). “We have made things much more flexible because we’ve done away with the controller box hardware and built the controller functionality into the tool itself. By having the tools directly integrated to their production system, manufacturers can now easily make production line changes and collect and report all the necessary data.”
Red Dot Award
The Red Dot Award is an international competition for product design, ranging from robot technology to vehicles and household aids. Each year, the award appraises the best products created in roughly 50 categories.
Meet our innovators
Tensor IxB Family
Main feature: User-friendly, ergonomic and lightweight battery nutrunners, offering powerful performance and accuracy.
Used at: Automotive,
aerospace and general industries around the world. Especially suitable for narrow production areas where a perfect result is crucial.
The new tool is also cordless and battery-powered, but still has a cable-tool level of productivity. It’s ideal for tight spaces, and the battery use cuts the overall energy consumption still further. The four-and-a-half-year development process has also improved the tool’s ergonomics, making it much easier to use for operators.
But it’s fair to say that the powerful in-built, integrated controller is the star of the show. So much so that it dazzled some customers who saw prototypes. It has also been awarded the prestigious Red Dot Design Award for 2021.
“When we presented the idea of having the controller inside, some people said ‘No, you cannot do that. The tool will be too heavy’,” says Tim. “And some customers who saw the first prototype said the controller couldn’t possibly be in there and was hidden somewhere!”
Such profound innovations take time and effort, but Tim and Jonas say all the teams involved – in Stockholm and customer centers worldwide – have been utterly committed to this “leap of faith.”
“This was probably the most complex product development process that we have ever entered into, both in terms of the technical challenges and the actual scale of it,” says Jonas. “It’s a complete program with different tools, a completely new software concept, new connectivity modes and a new battery platform.”
For those customers who still require wired connections, the controller box will continue to live for years to come, but the new technology is truly groundbreaking.
“It’s a historical transformation,” says Tim. “In a sense we’re now adding an option for our customers that’s the equivalent of changing from a fixed telephone line to a cell phone. It’s a new platform that will only keep growing in the future.”