Follow us on:
CONTACT US | Download the 2021/2022 issue | ©Atlas Copco AB
result
Search
A MAGAZINE FROM ATLAS COPCO GROUP
Sustainable technologies
Markets
Smart manufacturing
Our culture
Service and Consulting
Energy efficiency
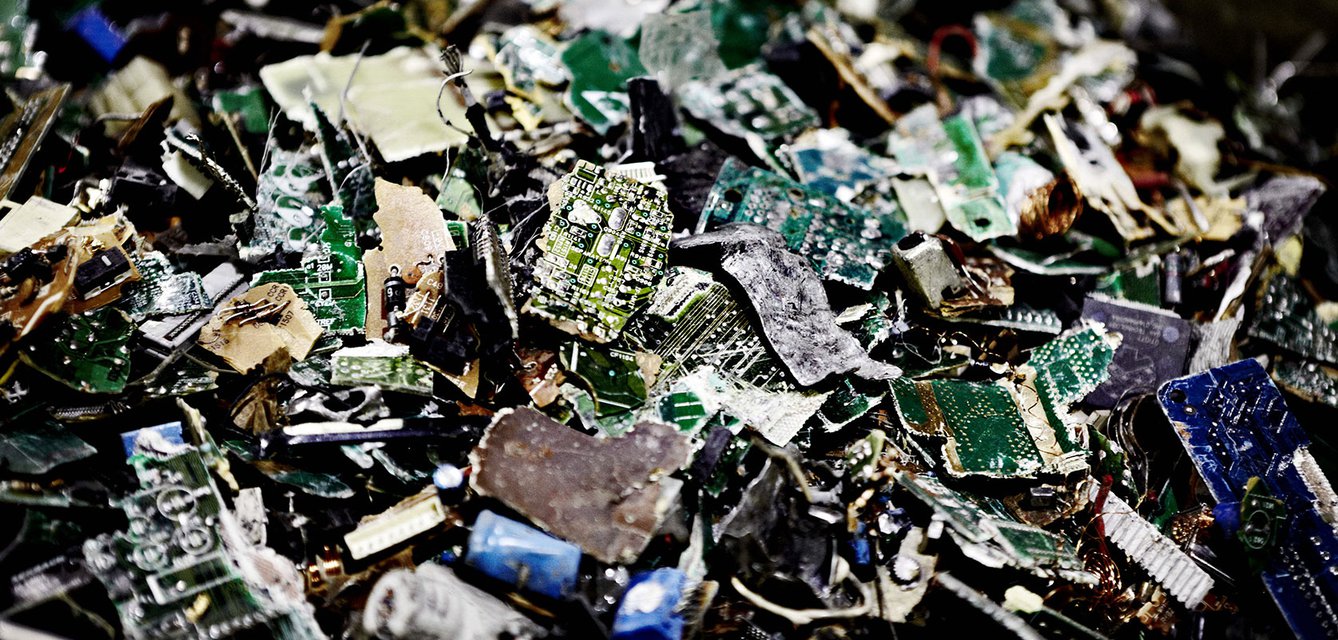
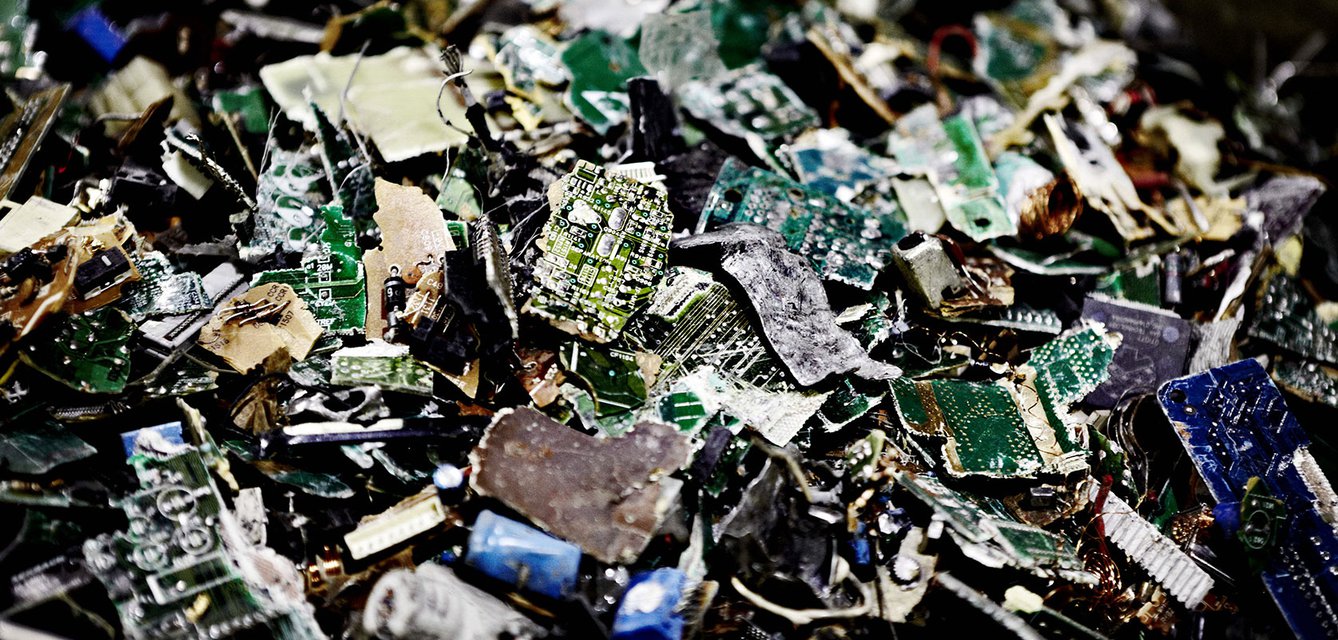
Part of the circular economy
Did you know that your mobile phone is a veritable gold mine? Boliden Rönnskär is one the world’s leading smelters for recovery of metals. Here circuit boards are converted into pure metal which can be used in new products. The process is energy intensive, but with the assistance of Atlas Copco the smelter is now on the right track to reduce its energy consumption by more than 1 million kWh per year.
Unlike many other materials, metals can be reused again and again without significantly losing their quality. Boliden Rönnskär in northern Sweden is one of the world’s leading players in electronics metal recycling, such as discarded mobile phones and circuit boards, and is thereby an important link in the circular economy. The smelter was founded as early as 1930 to process ore from nearby mines to pure metals, such as copper, silver and gold. Today it is one of the biggest and most efficient smelters in Europe.
Many of the smelter's processes require large amounts of compressed air, which puts high demands on energy efficiency and operational safety of the compressors. The smelter has strict internal requirements linked to carbon dioxide emissions and has, according to Swedish and European environmental legislation, also an obligation to minimize the impact on people and the environment by using the best possible technology.
In 2014 Boliden Rönnskär decided to change several old compressors to more energy efficient models. The old compressors worked well but the compressed air team suspected there was much to gain by changing the existing fixed speed machines to new models with variable speed drive (VSD).
To get a clear picture of the need for compressed air in the various sections of the production, the smelter decided to execute a so-called energy audit (AIRScan) together with Atlas Copco. Eleven different points for measuring compression and flow were installed in selected parts of the compressed air system. The measurement was carried out for two weeks while the smelter was fully operational.
The results were then analyzed by energy consultants from Atlas Copco. The analysis demonstrated that the existing compressed air facility was very energy efficient, well below the Swedish Energy Agency's guideline, but the compressed air team was right. By investing in VSD compressors and a central drive system the smelter could reduce its energy consumption by 850,000 kWh per year, as a first step. Considering the flow requirement, the compression and the available floor area, Atlas Copco presented a proposal where two model ZR500VSD VSD compressors replaced three older fixed speed machines.
Atlas Copco was also asked to perform a follow-up measurement after installation. It confirmed that energy consumption reduced as expected and that Boliden Rönnskär thereby not only saves money but also reduces its environmental footprint by the equivalent of 11 ton of carbon dioxide* per year. Total savings also included heavily reduced service costs.
Environment and sustainability have long been high on the list of Boliden Rönnskärs’ agenda, and the smelter is continuously investing in technology improvements. In 2022, another older fixed speed machine was replaced with a model ZR750 oil-free screw compressor. This has resulted in further energy savings of about 200,000 kWh per year and additionally, the service costs will be significantly reduced. After two or three years the entire machinery will be replaced and the smelter then expects to save more than 1 million kWh per year, compared to the situation before the first energy audit in 2014.
*The calculation is based the assumption of emissions of 13 g CO2 equivalents per kWh.
Photo credit: Boliden AB