Follow us on:
CONTACT US | Download the 2021/2022 issue | ©Atlas Copco AB
result
Search
A MAGAZINE FROM ATLAS COPCO GROUP
Sustainable technologies
Markets
Smart manufacturing
Our culture
Service and Consulting
Energy efficiency
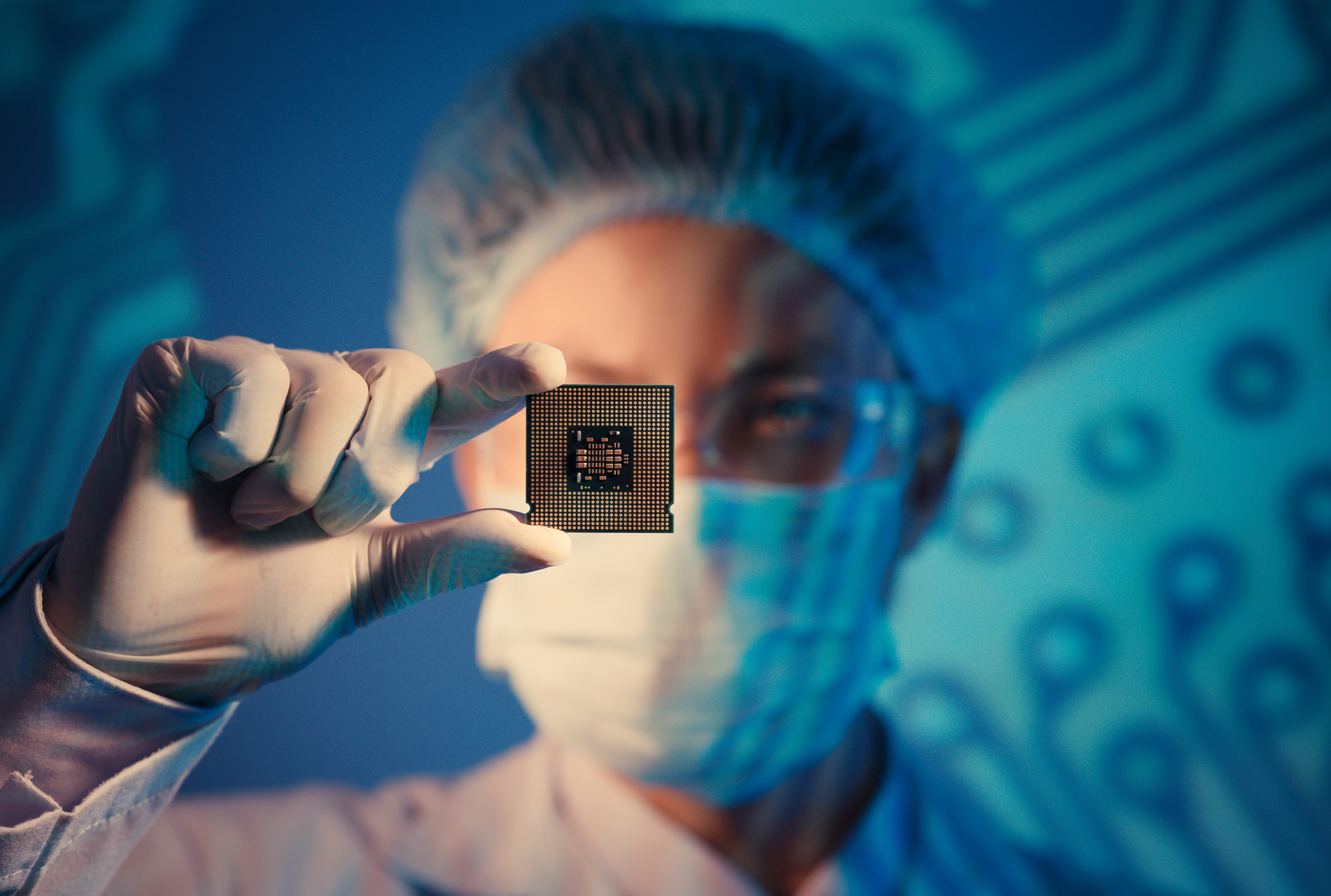
CHIPPING IN
FOR SAFETY
When a South Korean education center for semiconductor production experienced two severe explosions linked to nitrogen, they decided to replace their current machines with on-site nitrogen supply solutions from Atlas Copco.
Semiconductors make up the heart of modern-day electronics, and South Korea is at the heart of this industry. The world-leading semiconductor producers located here are constantly looking for highly skilled employees, and to meet this need, the Korea University of Technology and Education (Korea Tech) has established a top-notch education center in the city of Cheonan.
Each year, roughly 10,000 students pass through this Semiconductor Equipment Technology Education Center, as they are trained in semiconductor and solar cell production. The majority are undergraduate students, but the center also welcomes external trainees, researchers, teachers and people working at semiconductor manufacturing companies. The education center is rated number one in Korea, in terms of know-how and facilities.
As the trainings run all year round, the center must have 24/7 access to compressed air and nitrogen. Nitrogen plays a central role in the manufacturing of semiconductors. It is a very dangerous gas that can lead to asphyxiation. On top of this, it is highly explosive and it must be handled very carefully.
“Many schools and smaller research institutes use liquid nitrogen for cost reasons, but liquefied nitrogen is risky to handle. We prefer to have our own nitrogen generator on-site, and we believe it’s more cost-efficient as well,” says Cheolho Im, Technical Support Team Manager.
“We experienced two severe explosions in our lab. Fortunately, there were no casualties, but significant machine parts had to be replaced. Needless to say, safety and reliability are top priorities to us, so we decided to look for a new provider. While searching I found out that Atlas Copco not only provides air compressors but nitrogen generators as well. As we already had a very positive experience of their air compressors, we felt reliability was guaranteed,” says Cheolho Im.
In December 2019, the center installed an Atlas Copco nitrogen generator and a nitrogen supply compressor. In conjunction with the Atlas Copco oil-free air compressors already in use, the solution now provides nitrogen and compressed air to the ultra-clean semiconductor production rooms.
“With the new machine setup, even small amounts of compressed air show almost perfect purity,” says Chief Researcher Seokil Yoon. “It’s essential that oil and dust are filtered out properly. Any contamination can make the nitrogen generator and the connected pipeline explode. And if the lines leading to the semiconductor production are contaminated, all equipment must be replaced, which is both costly and time-consuming. With our new solution, this is no longer a problem.”