Follow us on:
CONTACT US | Download the 2021/2022 issue | ©Atlas Copco AB
result
Search
A MAGAZINE FROM ATLAS COPCO GROUP
Sustainable technologies
Markets
Smart manufacturing
Our culture
Service and Consulting
Energy efficiency
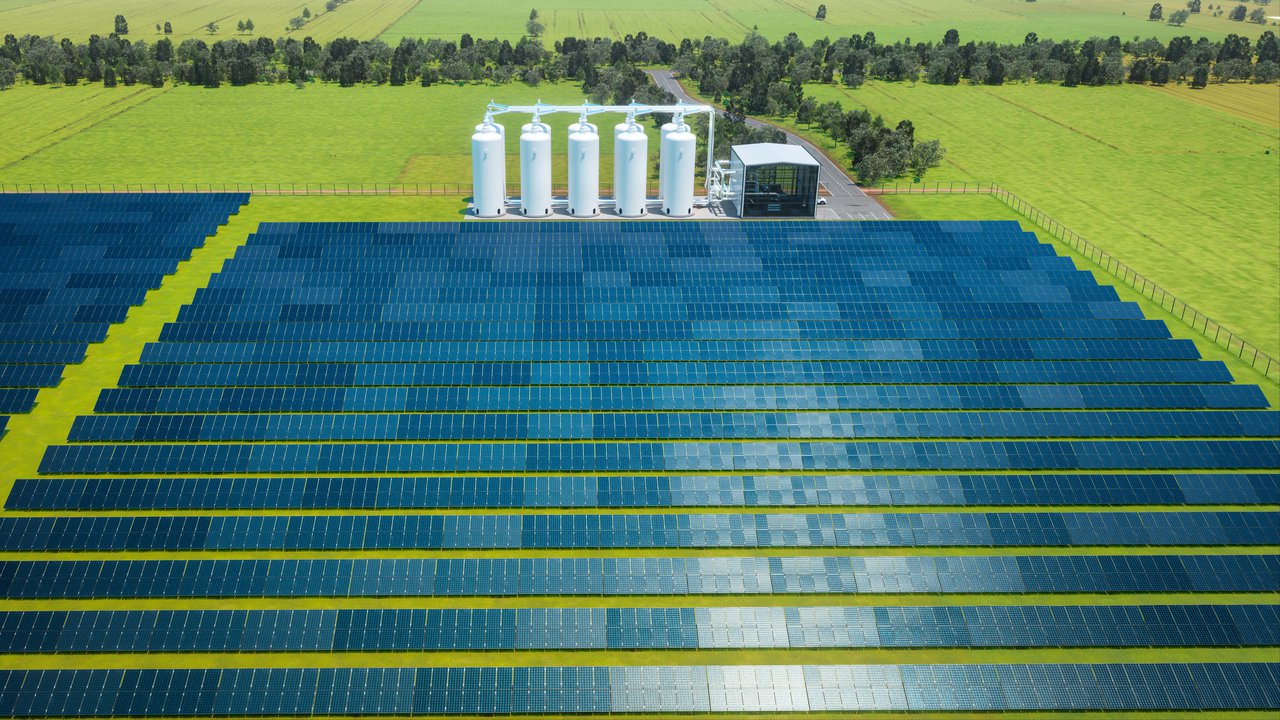
The missing link
In the move toward a carbon-free future, capturing renewable energy for later use is key. Danish company Stiesdal Storage Technologies is developing a groundbreaking thermal-based energy storage system that will allow the storage of electric energy for hours to weeks at a time. The company turned to Atlas Copco for the development of the turbo machinery needed in the process.
In many areas of the world, the transition to renewable energy is well underway. However, the production of clean and carbon-free electrical energy by means of wind and solar power will vary depending on the availability. Sometimes we produce too much energy and have to discard the excess; sometimes we need more energy than is available.
The challenge is to reduce the imbalances between energy demand and energy production.
Take Denmark, which derives 50% of its electricity from wind power harnessed by massive wind turbines:
“If we install 50% wind capacity, we would get around 45% contributed from wind power. But if 100% capacity was installed, we’d get just 60%,” says Bo Birkemose, The Chief Operating Officer of Danish climate technology company Stiesdal Storage Technologies, part of the Stiesdal Group.
“That’s because we don’t need all the energy when we produce it. We’re producing more than we need and have to shut it down, or we have situations where we can’t produce as much as we need.”
A proven concept with a new application
Stiesdal has a plan to tackle this issue. Their GridScale energy storage system is based on a simple technology that’s hundreds of years old: thermal energy storage.
Stiesdal’s solution is a pumped heat energy storage system that uses hot and cold crushed rock as a low-cost and carbon-free storage medium. The solution’s need for turbo-compressor and turbo-expander technology led Stiesdal Storage Technologies to Atlas Copco a couple of years ago.
“GridScale stores electricity into something that’s cheap and uncomplicated and which there is a lot of — stones,” explains Rasmus Rubycz, Market Manager for New Energy in Atlas Copco’s Gas & Process division and part of the Atlas Copco team working with Stiesdal Storage Technologies on this project.
“Lithium batteries are available and they’re getting cheaper all the time, but they’re only economically viable for less than 12 hours and are most efficient for just four hours,” Rasmus Rubycz adds.
Hydrogen could be an option for very large and long storage duration. However, the conversion efficiency is very low and storing hydrogen in its pure form is complicated and expensive on a large scale.
“Stiesdal’s solution eliminates the battery issue,” Rasmus continues. “It just needs steel, stone and minor insulation. It’s eco-friendly, using materials that are easily available, and it bridges the gap between batteries and hydrogen.”
“What was needed was something inexpensive and easy to manufacture, transport and install. We wanted it to be fully manufactured with a very short and simple commissioning and installation on site, just as with wind turbines,” says Bo Birkemose. “We’re not just developing a demonstration project. We know it works. Our solution can be ramped up on a large scale within a short time.”
An open and trusting collaboration
“We’re a small start-up company, even if we are well known in some industries. We’re also going out in some very new areas. One of the concerns people might have would be around the turbo machinery, so here we benefit from the expertise and recognition of Atlas Copco,” Bo Birkemose explains.
“When it comes to the strategic collaboration part, Atlas Copco also benefit from us because we bring experience from our decades of being front-runners in the wind industry. But what is very important here is that we as a small company can come to such a large organization and get into a good dialogue where we have a mutual respect for each other’s competencies. It’s a very open and trusting collaboration,” Bo Birkemose adds.
For Harald Dany, responsible for the Thermal Storage business line in Atlas Copco’s Gas & Process division, the collaboration is “a great story”.
“Stiesdal had this great idea but part of the technology they needed to realize it was missing. They were looking for a company that could support them to develop the machinery to bring this idea to fruition,” Harald says. “That’s where we come in. We support our customers to go beyond the technology and to develop it further based on the customer’s demands.”
What happens next?
The development process has taken place since 2019. Hanna Hörmeyer, Design Engineer in Atlas Copco’s Gas & Process division, explains that the main R&D challenges have revolved around the impact that the high operating temperatures can have on turbomachinery of this size.
“The challenge was to develop turbomachinery of this size for such high temperatures. It all started with the aerodynamic design, and we then started the mechanical design, where we focused on the impact that these high temperatures can have on the design and the material itself,” Hanna explains.
“There are many challenges to consider, but it’s a great option to use renewable energy much more efficiently. Here’s a very promising solution, that brings us one step closer to take better care of our planet. I’m really happy and excited to be working on this project.”
Stiesdal Storage Technologies aims to install prototype plants in a number of global locations in 2022, before the first commercial iteration in 2023. The first demonstration plant is currently being set up on Lolland, a renewables-rich island off Denmark in the Baltic Sea, and will be charged with surplus power from wind and solar farms on the island.
Bo Birkemose sees a number of different customer segments, for example in remote locations far from grids, such as wind farms far from populations, or in mines that currently rely greatly on diesel generators.
“The beauty of our choice of technology is actually its lack of technology,” says Birkemose. “This is a proven concept that can be scaled up in a short time. What gets us up in the morning is the knowledge that the technologies we are working on will make a significant contribution to a better and cleaner future.”
GridScale can best be illustrated as a heat pump system that moves energy between a variable number, depending on chosen capacity, of separate reservoirs to store heat and cold, respectively.
Since the maximum temperature of the cold storage reservoir is much lower than in the hot storage reservoir, the cold reservoir can use basically any type of crushed rock. For the hot storage, the only requirement is the ability to withstand high temperatures which many rock types can do.
There is no degradation of the crushed rock storage materials, and the GridScale nameplate storage capacity is available for the full lifetime of the system.
The GridScale range covers both the 12 to 18-hour duration required for day-to-day smoothing of solar power, and the three to seven-day duration required for the smoothing of wind power over gaps caused by low wind periods.
“Taking Denmark as the example, if we install one day’s capacity of thermal storage, we raise the usable amount of power to 75%,” says Stiesdal Storage Technologies’ COO Bo Birkemose.