Follow us on:
CONTACT US | Download the 2021/2022 issue | ©Atlas Copco AB
result
Search
A MAGAZINE FROM ATLAS COPCO GROUP
Sustainable technologies
Markets
Smart manufacturing
Our culture
Service and Consulting
Energy efficiency
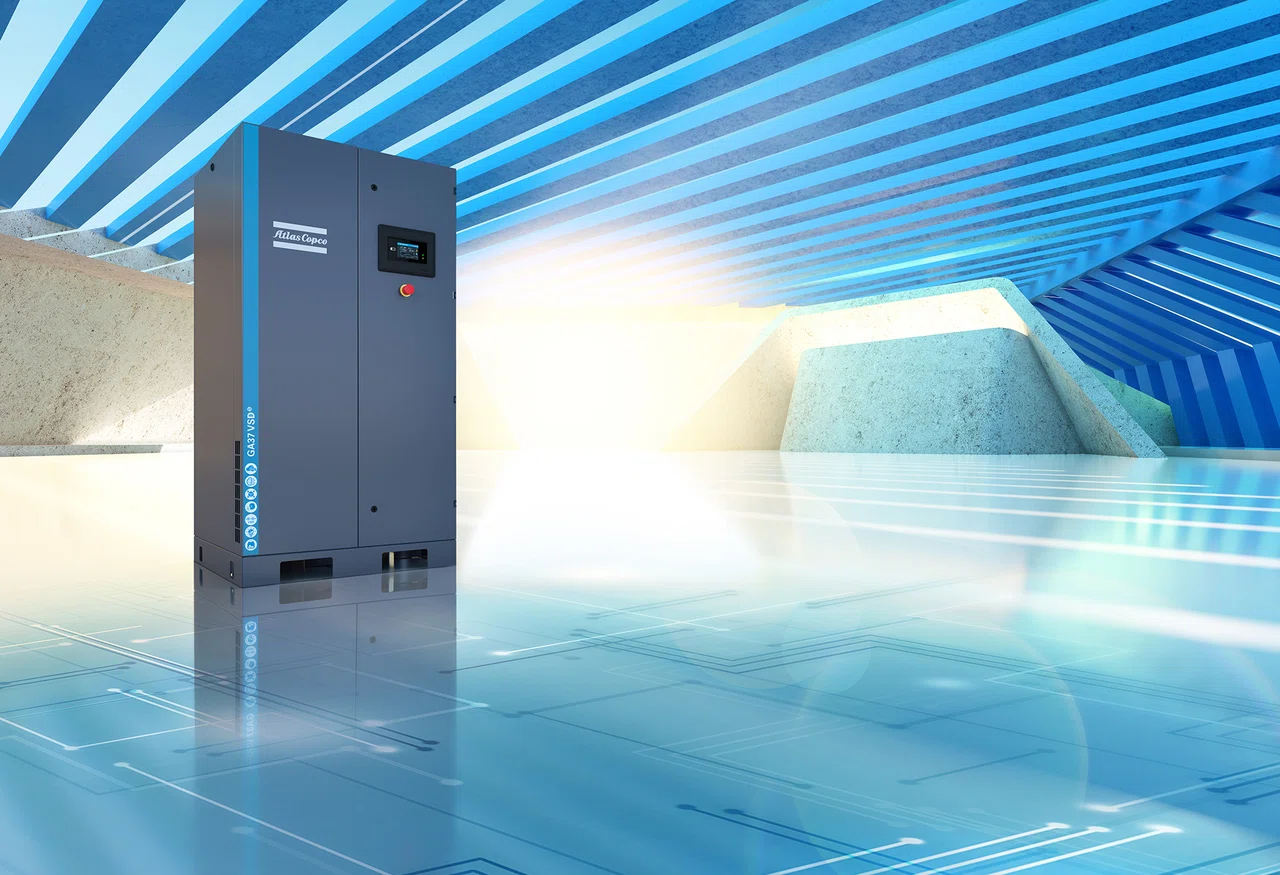
The energy-efficient
trailblazer
How do you update a compressor that’s still the market leader, eight years after its launch? It takes an innovation leap based on smart and sustainable technology.
Since its launch in 2013, Atlas Copco’s GA VSD+ compressor range has been hailed for its extraordinary energy efficiency, small footprint, and low total cost of ownership. With its highly efficient drivetrain and variable speed drive, it’s still the market-leader in its class and a vital piece of equipment for the likes of the general manufacturing industries, textiles, pharmaceuticals and the chemical industry.
Variable speed drive (VSD) technology enables a motor to adapt to the current demand, which translates into substantial energy-savings. In 1994, Atlas Copco was the first supplier to integrate this technology into compressors, and in 2013 a new industry standard was set with the in-house innovation of VSD+, taking energy consumption to a record low.
However, a technology leader must never rest on its laurels.
“If you stand still there’s a risk of someone else catching up,” explains Jan Vansweevelt, Product Manager in Atlas Copco’s Industrial Air division and responsible for the project that developed the new GA 22-37 VSDs compressor range that was unveiled in October 2021.
A third generation
The story of the third generation of VSD compressors started in 2018, when a combination of increased sustainability requirements from customers and insights based on real-time machine data initiated a development process.
“We’ve had our compressors connected for many years, and it helps us to see the different ways our machines are used worldwide,” says Jan Vansweevelt. “We now have a global machine park of 200,000 connected units, which gives us access to a well of data that we use to drive innovation based on our customer’s daily operations.”
For example, the data showed that a substantial number of customers were running their machines at speeds for which it was not optimized.
“The normal optimal point for a VSD+ machine is between 60 and 80% of its maximum speed, but thanks to the data we found out that many customers were actually running their machines in the 20-60% zone. The VSD+ is not designed to perform at its best in these conditions, so in some cases the performance dipped,” Jan Vansweevelt explains.
When the development team combined data-based insights with their own R&D ideas, a clear picture emerged. The nature of the changes meant the existing VSD+ compressor range couldn’t be updated. It was time for a new generation.
“The ‘aha!’ moment was when we realized that if we wanted to make an even better machine, it had to become smarter,” says Jan Vansweevelt.
Smart and sustainable savings
The main selling point of the VSDs technology is its ability to automatically adapt to any change in the ambient conditions in which it’s being used. So, if you need to run it at a lower speed, or if it is working under humid conditions with varying ambient temperatures, the built-in algorithms will adjust the set points accordingly to ensure it maximizes the performance for each application.
There is also a unique boost flow mode if the compressed air demand exceeds the machine’s maximum capacity. The compressor will then check the ambient conditions and its internal parameters, and if all is okay, it will temporarily deliver more air.
“The big benefit here is that instead of being confronted with pressure drops in their system, our customers can rely on the VSDs to keep things running while we analyze their needs and help them find a more sustainable solution,” explains says Jan Vansweevelt.
A double savings and sustainability aspect comes from increased energy efficiency, with a reduced energy consumption up to 60% compared with fixed-speed models, and additional energy savings with up to 80% heat recovery.
“We did the calculation for a 37 kW machine, where we found there is potential to reduce 60 tonnes of CO2 emissions per year per machine, compared to a traditional fixed speed compressor. That’s like taking 14 passenger cars off the road – for every single new machine. So, by working together with our customers we can contribute to a better tomorrow,” says Jan Vansweevelt.
We now have a global machine park of 200,000 connected units, which gives us access to a well of data that we use to drive innovation based on our customer’s daily operations.”
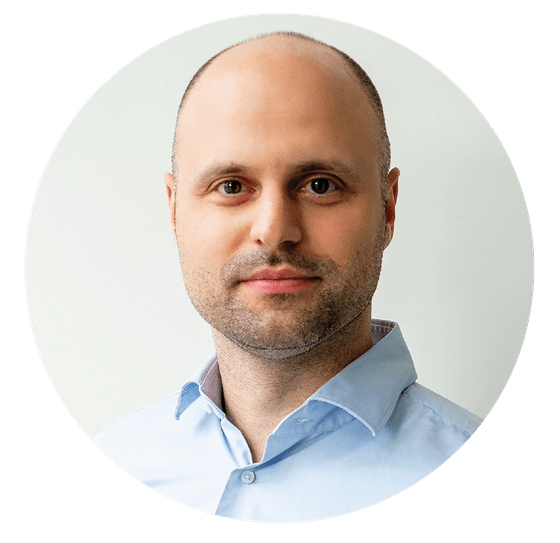
Jan Vansweevelt,
Product Manager,
Atlas Copco’s Industrial Air division
Atlas Copco’s Industrial Air division